Rapid Prototyping Injection Molding: Revolutionizing Manufacturing Processes
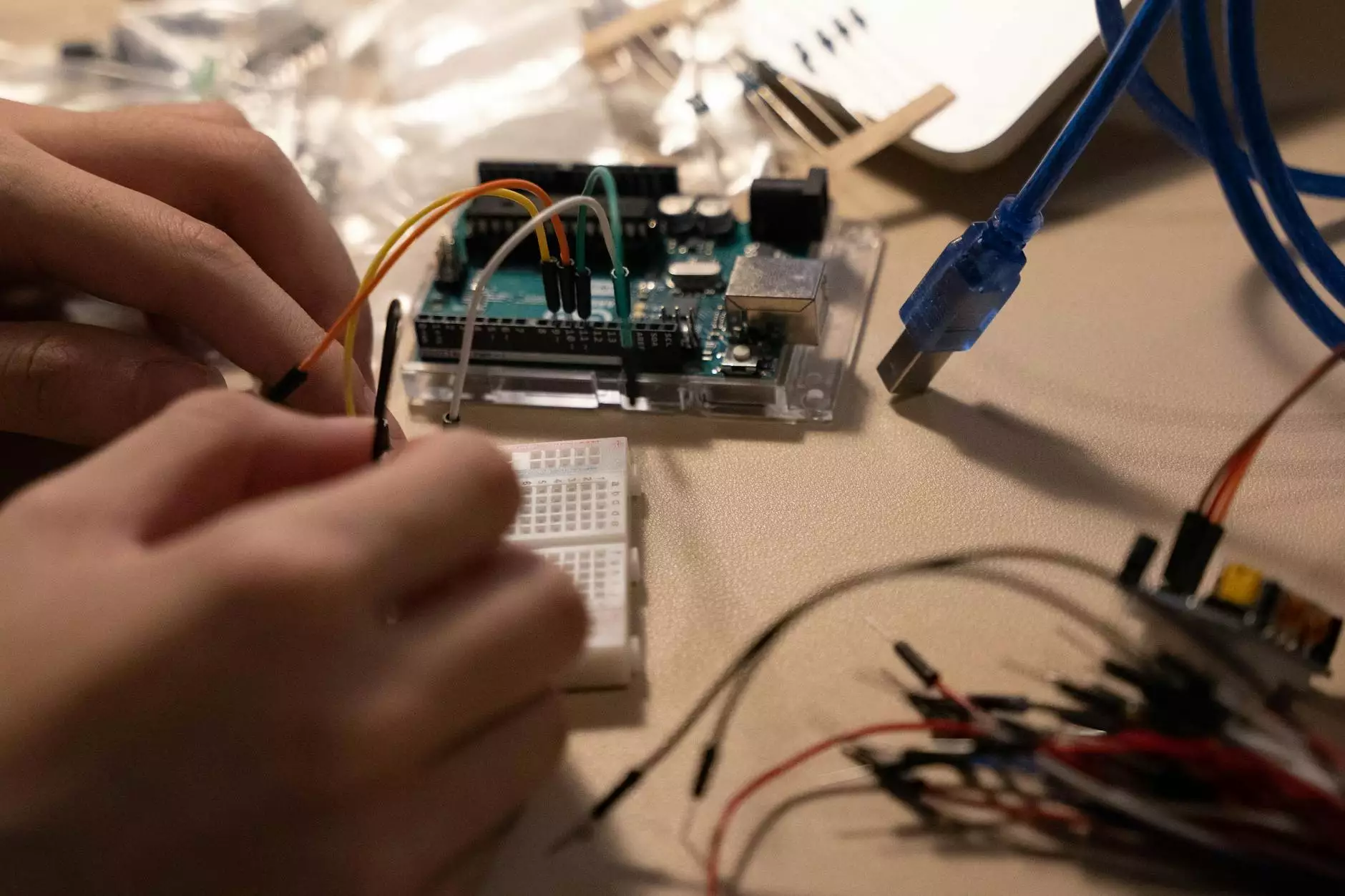
In the ever-evolving landscape of manufacturing, rapid prototyping injection molding has emerged as a transformative technology. It addresses the growing demand for faster product development, lower costs, and greater design flexibility. In this article, we will explore the intricacies of rapid prototyping injection molding, its benefits for metal fabricators, and how it can significantly enhance the production processes.
Understanding Rapid Prototyping Injection Molding
To fully appreciate the advantages of rapid prototyping injection molding, it is essential to understand what it entails. This process combines traditional injection molding techniques with rapid prototyping methods to create high-quality prototypes efficiently.
What is Injection Molding?
Injection molding is a manufacturing process for producing parts by injecting molten material into a mold. This technique is widely used for making parts from thermoplastic and thermosetting plastic materials. The benefits of injection molding include:
- High Efficiency: Rapid production rates allow for mass manufacturing.
- Precision: Capable of producing complex shapes with high tolerances.
- Material Variety: Compatible with a wide range of materials, including plastics and metals.
The Concept of Rapid Prototyping
Rapid prototyping refers to the quick fabrication of a scale model of a physical part using three-dimensional computer-aided design (CAD) data. Various techniques, such as 3D printing and CNC machining, are utilized to create prototypes that can be used for testing and validation purposes.
Benefits of Rapid Prototyping Injection Molding
The integration of rapid prototyping with injection molding has brought several benefits that are crucial for businesses, particularly in the metal fabrication sector.
1. Accelerated Product Development
One of the most significant advantages of rapid prototyping injection molding is the reduction in development time. Traditional methods can take weeks or even months to bring a product from conception to production. However, with rapid prototyping, manufacturers can have a prototype ready in days, allowing for quicker iterations and refinements.
2. Cost Efficiency
Developing a prototype through traditional methods often involves high costs associated with tooling and adjustments. Rapid prototyping injection molding minimizes these costs by allowing designers to test multiple designs without incurring excessive expenses on molds or materials.
3. Enhanced Design Flexibility
With rapid prototyping, designers can experiment with various iterations of their designs without the time-consuming processes typically associated with traditional injection molding. This flexibility encourages innovation and leads to better-performing products.
4. Improved Accuracy and Quality
Rapid prototyping techniques can achieve higher levels of precision compared to other prototyping methods. This increased accuracy translates to a better fit for components when they enter the final stage of production, thus enhancing the overall quality of the product.
Applications of Rapid Prototyping Injection Molding
The versatility of rapid prototyping injection molding is evident across various industries. Below are some key applications:
1. Automotive Industry
The automotive sector leverages rapid prototyping injection molding for designing components such as dashboards, interior parts, and intricate design elements. The technology enables automotive manufacturers to test parts under real-world conditions before committing to full-scale production.
2. Aerospace Sector
In aerospace, precision is paramount. Rapid prototyping allows for the testing of complex geometries required for various components, ensuring that they meet stringent safety and performance standards.
3. Consumer Electronics
Consumer electronics companies utilize rapid prototyping injection molding to develop enclosures, buttons, and various structural components rapidly. This technology supports quick changes in design according to market trends or consumer feedback.
4. Healthcare
The healthcare industry benefits significantly from rapid prototyping, especially in creating customized implants and prosthetics. The ability to quickly produce and modify prototypes can lead to better patient outcomes through tailored solutions.
Implementing Rapid Prototyping Injection Molding in Your Business
For those interested in adopting rapid prototyping injection molding, here are the steps to consider:
1. Evaluate Your Needs
Assess your production processes and determine how rapid prototyping can integrate into them. Identify the products that could benefit from quicker iteration and testing.
2. Invest in Technology
Investing in state-of-the-art equipment that supports both injection molding and rapid prototyping techniques is crucial. This includes high-quality 3D printers and advanced injection molding machines.
3. Collaborate with Experts
Partnering with experienced engineers and designers can streamline the transition to rapid prototyping injection molding. Their expertise will help ensure that your operations are efficient and productive.
4. Continuous Improvement
Embrace a culture of continuous improvement within your organization. This means regularly evaluating the prototypes and products you develop and making adjustments based on feedback.
Challenges and Solutions in Rapid Prototyping Injection Molding
While the advantages are numerous, there are also challenges associated with rapid prototyping injection molding. Here, we address some common issues and their solutions.
1. Material Limitations
Some materials may not be suitable for rapid prototyping methods. Solution: Research and develop a portfolio of materials that cater to your product requirements. Explore alternative materials that can withstand the injection molding process.
2. Initial Costs
The initial investment in technology can be high. Solution: Plan for a phased approach to investment and consider leasing equipment or working with a third-party service provider to minimize upfront costs.
3. Learning Curve
Transitioning to new technologies requires training staff and adjusting workflows. Solution: Provide comprehensive training sessions and develop resources for employees to facilitate the adoption process smoothly.
The Future of Rapid Prototyping Injection Molding
As technology advances, the potential for rapid prototyping injection molding continues to expand. With innovations such as AI-driven design and improved material science, manufacturers can expect even faster, more efficient production processes.
1. Sustainability
Future developments in rapid prototyping will likely focus on sustainability. Using biodegradable materials and minimizing waste during the prototyping process will become crucial.
2. Advanced Simulation Technologies
Enhanced simulation tools will allow manufacturers to predict and evaluate how prototypes will perform in real-world conditions, further refining the design process before moving to production.
3. Increased Customization
Consumer demand for customized products will push manufacturers to adopt rapid prototyping methods to satisfy this trend, leading to more bespoke solutions in various industries.
Conclusion
In conclusion, rapid prototyping injection molding represents a significant leap forward in manufacturing technologies, particularly for metal fabricators. Its ability to accelerate product development, reduce costs, and enhance design flexibility makes it a vital asset for businesses aiming to stay competitive in the fast-paced manufacturing landscape. By embracing this innovative technology, manufacturers can drive efficiency, improve product quality, and ultimately meet the ever-changing demands of consumers.
For those interested in exploring rapid prototyping injection molding services, visit DeepMould.net to learn more about how they can help transform your manufacturing processes.