Revolutionizing Products Through Plastic Molding for Electrical Applications
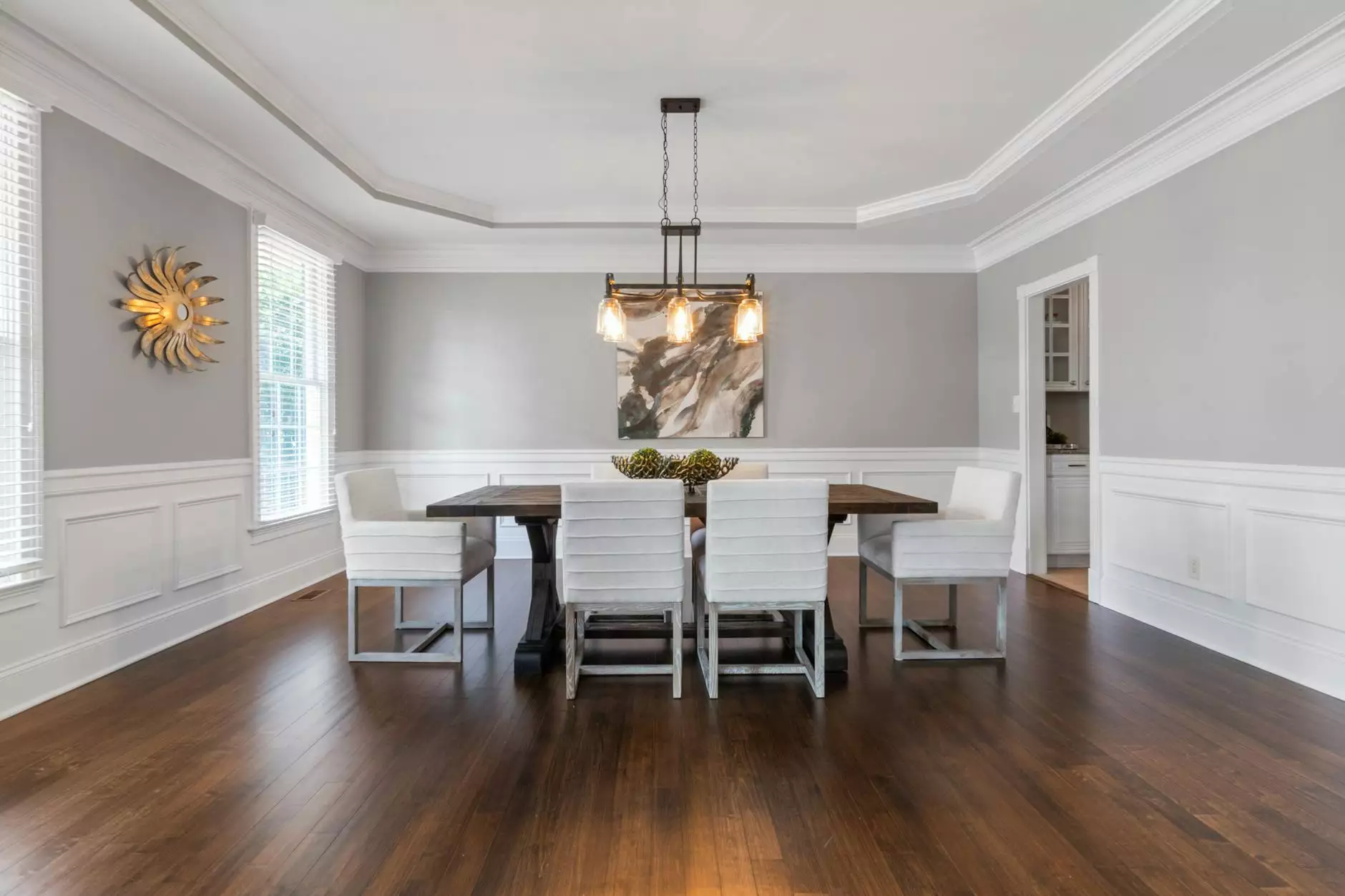
In the ever-evolving landscape of manufacturing, plastic molding for electrical components has emerged as a critical technology that enhances not only the functionality but also the aesthetic appeal of various products. This method, which combines innovative engineering with modern polymers, is shaping the future of electrical equipment design and production. In this extensive article, we will delve into the intricate world of plastic molding, examine its applications, and explore how it stands as a cornerstone for modern electrical products.
The Basics of Plastic Molding
Plastic molding is a manufacturing process that transforms raw plastic materials into desired shapes through heat and pressure. This technique is fundamental to creating intricate components used in various industries. The most prevalent types of plastic molding include:
- Injection Molding: A process where molten plastic is injected into a mold and allowed to cool, solidifying into the final product.
- Blow Molding: Typically used for hollow objects, this technique involves inflating heated plastic within a mold.
- Rotational Molding: This method is used for large, hollow objects, where a resin is heated and rotated within a mold.
Why Choose Plastic Molding for Electrical Components?
The choice of plastic molding for electrical applications offers several notable advantages:
1. Lightweight and Durable
Plastics provide an excellent alternative to heavier materials like metals. The use of plastic molding for electrical components results in lightweight products that are easier to handle while maintaining durability. The robust nature of modern plastic blends ensures that these components can withstand demanding environments.
2. Cost-Effectiveness
With the potential for reduced material costs and lower labor expenses, plastic molding is often a more economical choice than traditional manufacturing processes. The efficiency of the molding process allows for high-volume production, significantly driving down costs per unit.
3. Design Flexibility
Plastic molding allows for intricate designs that may be challenging to achieve with metal. The ability to mold complex geometries means that products can be designed with both functionality and aesthetics in mind. Customization is straightforward, enabling manufacturers to produce unique product lines tailored to specific market needs.
4. Enhanced Electrical Insulation
Many plastic materials exhibit excellent insulating properties. This is a crucial characteristic for electrical applications where preventing accidental conduction is essential for safety. The use of plastics helps ensure that electrical components meet stringent regulatory standards.
Applications of Plastic Molding in Electrical Equipment
The versatility of plastic molding for electrical components extends across several domains. Here are some prominent applications:
1. Wiring and Cable Insulation
Plastic molding plays a pivotal role in the insulation of wiring and cables. It provides protection against environmental factors and mechanical damage. Various types of plastics, such as PVC and polyethylene, are widely used due to their excellent insulating properties.
2. Connectors and Switches
In electrical devices, connectors and switches are essential for functionality. Plastic molded components can be produced to precise specifications, ensuring that these parts fit seamlessly into electronic assemblies. Additionally, styles and colors can be customized to fit branding requirements.
3. Enclosures and Housings
The enclosures for circuit breakers, control systems, and other electrical equipment benefit from plastic molding. These housings safeguard internal components from external elements while also providing an aesthetic appeal. Properties such as UV resistance and flame retardance can be integrated into the material selections, enhancing safety.
4. Appliance Components
From washing machines to kitchen electronics, many household appliances incorporate plastic molded parts. The lightweight nature of plastic facilitates efficient shipping and installation while offering robust protection for internal mechanisms.
Innovations in Plastic Molding Technology
As technology continues to advance, the methods and materials used in plastic molding are also evolving. Key innovations include:
1. Use of Sustainable Materials
With the rise of environmental consciousness, manufacturers are increasingly turning to biodegradable and recyclable plastics. This shift not only meets regulatory requirements but also appeals to eco-conscious consumers.
2. 3D Printing and Rapid Prototyping
The intersection of 3D printing and traditional molding methods allows for rapid prototyping, which significantly accelerates the design process. This technology enables manufacturers to test and refine product concepts before committing to mass production, thereby reducing time-to-market.
3. Smart Molding Techniques
Integration of smart sensors into the molding process enables real-time monitoring and data collection, enhancing quality control. These innovations help improve product consistency and reliability, essential characteristics in electrical applications.
Choosing the Right Partner for Plastic Molding
Finding a reliable partner for your plastic molding for electrical needs is crucial for success. Consider the following attributes when selecting a manufacturer:
- Experience: Look for a company with extensive experience in the industry, particularly with electrical components.
- Advanced Capabilities: Ensure that the manufacturer possesses state-of-the-art technology and facilities to accommodate your specific requirements.
- Quality Assurance: Investigate their quality control measures to guarantee that your products will meet industry standards.
Conclusion
In summary, plastic molding for electrical applications represents a vital component of modern manufacturing. Its multitude of benefits—including lightweight durability, cost-effectiveness, design flexibility, and enhanced insulation—positions plastic molding as an ideal solution for various electrical products. As technological advancements continue to emerge, the potential for innovation in this field is boundless. Choosing the right partner, such as Deep Mould, can further enhance production capabilities and lead to remarkable advancements in electrical design and manufacturing.
Embrace the future of manufacturing with plastic molding, and witness how this remarkable technology can elevate your products to new heights!