Understanding GRP Manufacturers: Innovations in Composite Materials
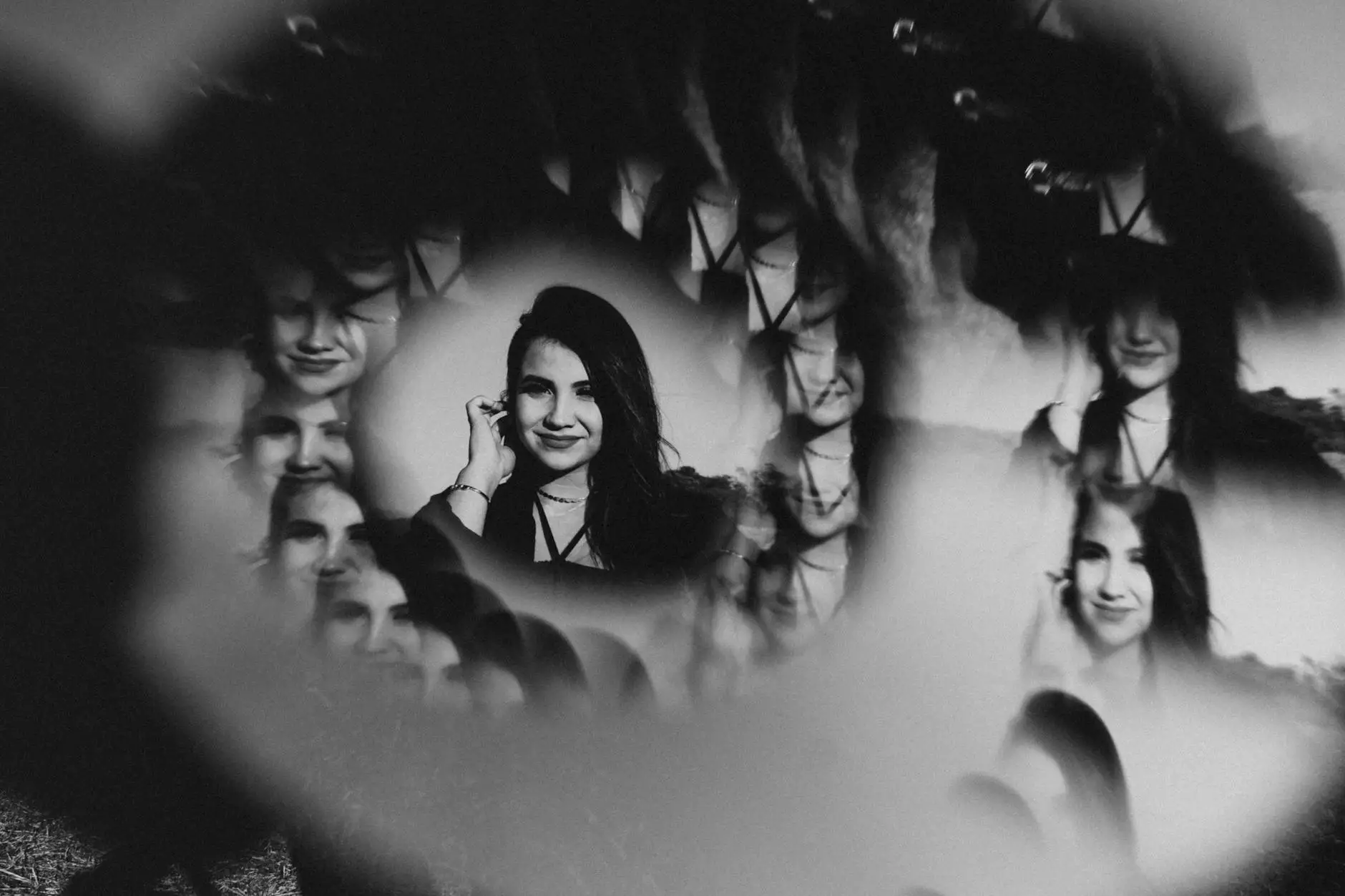
What is GRP?
Glass Reinforced Plastic (GRP), also known as Glass Reinforced Polymer, is a composite material made from a polymer matrix
The Role of GRP Manufacturers
GRP manufacturers play a pivotal role in the advancement of composite materials. By utilizing advanced techniques in engineering, design, and production, they create products that meet the diverse needs of industries ranging from construction to aerospace.
The Manufacturing Process
The production of GRP involves several critical steps, each designed to optimize performance and durability:
- Design & Engineering: This initial phase involves computer-aided design (CAD) and simulations to create optimal models.
- Material Selection: High-quality resins and glass fibers are selected based on the specific requirements of the final product.
- Molding: Various molding techniques (such as hand lay-up, spray-up, and pultrusion) are employed to shape the composite material.
- Curing: The molded parts undergo a curing process to harden and achieve the desired structural integrity.
- Finishing: Final touches include trimming, sanding, and surface treatment to enhance aesthetics and performance.
Benefits of Using GRP
When considering the materials for various applications, GRP offers several compelling benefits:
- Lightweight: GRP components are significantly lighter than metal alternatives, which can lead to lower transportation costs and easier handling.
- Corrosion Resistance: GRP is inherently resistant to a wide range of chemicals, making it an ideal choice for environments exposed to harsh substances.
- Durability: With excellent tensile strength and impact resistance, products manufactured from GRP can withstand significant stresses and strains.
- Versatility: GRP can be molded into virtually any shape, allowing for limitless design possibilities across various industries.
- Thermal Insulation: This material has superior thermal insulation properties, making it suitable for applications where temperature management is critical.
Applications of GRP
GRP is used in numerous industries due to its vast array of benefits. Here are some key applications:
Aerospace
In the aerospace sector, GRP is utilized for lightweight structural components, helping to improve fuel efficiency and reduce overall weight without sacrificing strength.
Construction
GRP is extensively used in the construction industry for architectural elements, roofing systems, and flooring solutions due to its durability and aesthetic appeal.
Marine
Marine applications benefit from GRP’s corrosion resistance and ability to handle the harsh marine environment, making it ideal for boat hulls and other components.
Automotive
In the automotive industry, GRP is employed for parts that require a combination of lightness and strength, contributing significantly to energy efficiency and performance.
Electrical and Telecommunications
GRP is also used in the manufacturing of enclosures and protective casings for electrical and telecom equipment, providing excellent insulation and protection from environmental factors.
Leading GRP Manufacturers: A Focus on Celtic Composites
Among the prominent GRP manufacturers, Celtic Composites stands out for their commitment to quality and innovation. With a team of expert engineers and state-of-the-art technology, they produce an array of composite products tailored to meet the demanding requirements of their clients.
Why Choose Celtic Composites?
Here are several reasons why Celtic Composites is a leader in the GRP manufacturing sector:
- Expertise: With years of experience in the industry, their team understands the complexities of GRP applications and consistently delivers high-quality solutions.
- Customization: Celtic Composites offers bespoke solutions tailored to meet specific client needs, ensuring optimal results and satisfaction.
- Environmental Commitment: Celtic Composites prioritizes sustainability in their manufacturing processes, incorporating eco-friendly practices without compromising on quality.
- Comprehensive Service: From initial consultation through to after-sales support, their customer-centric approach ensures a seamless experience for clients.
Future Trends in GRP Manufacturing
As technological advancements continue to shape the manufacturing landscape, several trends are emerging within the field of GRP production:
1. Automation and Digitalization
The integration of automated processes and digital technologies will streamlining manufacturing and improving operational efficiency, enabling GRP manufacturers to meet increasing demand.
2. Enhanced Materials
Research and development efforts focus on creating new formulations for resins and glass fibers that enhance the properties of GRP, such as improved strength-to-weight ratios and thermal stability.
3. Sustainable Practices
As industries shift towards greener practices, GRP manufacturers are likely to embrace sustainable materials and eco-friendly production methods, contributing to a reduction in environmental impact.
4. Expansion of Applications
New applications for GRP are constantly being discovered, with innovations finding their way into diverse sectors such as biomedical engineering and renewable energy. This trend is set to expand further as our understanding of composite materials grows.
Conclusion
In conclusion, GRP manufacturers like Celtic Composites are at the forefront of material innovation, providing solutions that meet the evolving needs of various industries. Their focus on quality, customization, and sustainable practices positions them as leaders within the composite materials sector. As the demand for innovative, durable materials continues to grow, GRP manufacturers will undoubtedly play an essential role in shaping the future of manufacturing.